ในโรงงานผลิตชิ้นส่วนยานยนต์ ประเภทปั๊มขึ้นรูปโลหะ
ประวัติความเป็นมาของกิจการ
บริษัทผู้ผลิตชิ้นส่วนรถยนต์และรถจักรยานยนต์ในกลุ่มธุรกิจประเภท OEM กระบวนการหลักคือการปั๊มขึ้นรูปโลหะแผ่น (Stamping) งานเชื่อมโลหะ (Welding) และการประกอบ (Sub assembly) บริษัทมีพนักงาน 130 คน โดยเป็นพนักงานในสายการผลิต 90 คน
ในการที่จะทำกิจกรรม TPS จะเริ่มจากการคัดเลือกผลิตภัณฑ์ที่จะทำเป็นสายการผลิตต้นแบบ (Model line) โดยจะพิจารณาชิ้นงานที่มีความต้องการสม่ำเสมอ มีจำนวนกระบวนการที่มากพอสมควร และที่สำคัญคือเป็นชิ้นงานที่ผู้บริหารให้ความสำคัญกับการแก้ปัญหาในเรื่อง ของ lead time ยาวนาน จากการพิจารณาร่วมกันของทีมงานได้คัดเลือกชิ้นงานทั้งหมด 5 รุ่นมาทำเป็น Model line ดังภาพ
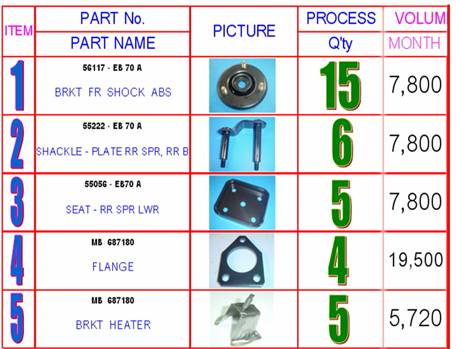
กระบวนการที่เกี่ยวข้องกับชิ้นงานใน Model line จะมีลำดับดังนี้
การทำกิจกรรม TPS จะดำเนินการอย่างมีขั้นตอนโดยจะเริ่มตั้งแต่
1. กิจกรรม Worksite Control คือ การปรับสภาพการทำงานหน้างานให้เหมาะสม สามารถควบคุมได้ด้วยสายตา ซึ่งเมื่อทำกิจกรรมในช่วงนี้เสร็จทำให้พื้นที่ของ Model line มีความเป็นระเบียบ สามารถค้นพบสิ่งผิดปกติได้โดยง่าย สถานที่ทำงานอยู่ภายใต้การควบคุมทั้งในเรื่องของวิธีการทำงาน เครื่องจักร คุณภาพ ผลผลิต กำลังคน และที่สำคัญที่สุดคือความปลอดภัย
2. กิจกรรม Continuous Flow คือ การทำให้การผลิตชิ้นงานสามารถไหลได้อย่างต่อเนื่อง ด้วยการจัดเรียงเครื่องจักรและกระบวนการผลิตให้สามารถผลิตชิ้นงานตั้งแต่ เริ่มต้นจนเสร็จเป็นชิ้นงานสำเร็จได้อย่างต่อเนื่องโดยให้มีจุดที่ชิ้นงาน ต้องหยุดชะงักให้น้อยที่สุด ขั้นตอนจะเริ่มจากการวิเคราะห์การไหลของวัตถุดิบ
โดยใช้แผนภาพการไหลของวัตถุดิบ (Material Flow Chart) ซึ่งพบว่าการไหลของวัตถุดิบมีความซับซ้อนมาก เนื่องจากกระบวนการอยู่ห่างไกลกัน และไม่มีการเรียงเครื่องจักรตามลำดับกระบวนการ จากนั้นจึงวางแนวทางปรับปรุงโดยร่าง MFC ที่เป็นเป้าหมายในการปรับปรุงขึ้นมา แล้วทำการปรับปรุง Layout ของเครื่องจักรใหม่ ทำให้ชิ้นงานสามารถไหลได้อย่างต่อเนื่องตั้งแต่กระบวนการแรกจนถึงกระบวนการ สุดท้าย ส่งผลทำให้ Lead time ที่เกิดขึ้นใน Process ได้จาก 17 วัน เหลือ 4 วัน, Stock in Process ได้จาก 10,000 ชิ้น เหลือ 1,200 ชิ้น
ภาพ Model line หลังจากทำการย้าย layout และเชื่อมต่อกระบวนการด้วยรางส่งชิ้นงาน (Chuter)
3. กิจกรรม Standardized Work คือ การศึกษาการทำงานของพนักงาน สร้างเป็นงานมาตรฐานซึ่งจะทำให้พนักงานผลิตสินค้าอย่างมีคุณภาพด้วยความสม่ำ เสมอและปลอดภัย โดยการเขียนงานมาตรฐานต้องคำนึงถึงความเร็วในการขาย (Sales speed) ที่ถูกแปลงมาให้อยู่ในรูปของ Takt time (T/T) แล้วทำการปรับปรุงงานมาตรฐานนั้นให้การทำงานของพนักงานมีประสิทธิภาพสูงสุด ภายใต้ T/T ขั้นตอนเริ่มจากการศึกษาเวลา นำมาเขียนเอกสารงานมาตรฐาน (San-ten set) ซึ่งประกอบด้วย ตารางประสิทธิภาพกระบวนการผลิต ตารางงานมาตรฐานผสม และแผนภาพงานมาตรฐานโดย
เอกสารเหล่านี้จะถูกทำขึ้นสำหรับพนักงานแต่ละคนเพื่อให้ยึดถือเป็นข้อปฏิบัติในการทำงาน จากนั้นนำข้อมูลการจับเวลามาทำการ Balance งานโดยใช้ Yamazumi Chart จะทำให้การแบ่งงานเป็นไปอย่างมีประสิทธิภาพส่งผลให้สามารถทำงานได้ตามที่ ลูกค้าต้องการด้วยจำนวนคนที่น้อยลง จากเดิมที่ใช้พนักงานปฏิบัติงาน 14 คนลดลงเหลือ 11 คน และการลดเวลาในการ Set up ส่งผลให้ Productivity เพิ่มขึ้นอีก 74.44%
4. กิจกรรม Pull System คือ การเปลี่ยนระบบการผลิตที่มีอยู่เดิมให้กลายเป็นระบบการผลิตแบบดึง ซึ่งเป็นระบบการผลิตที่เริ่มจากความต้องการของลูกค้าเป็นหลัก โดยที่กิจกรรมการผลิตทั้งหมดในโรงงานจะเริ่มก็ต่อเมื่อลูกค้าดึงของที่ต้อง การจากคลังสินค้า จากนั้นข้อมูลความต้องการสินค้าที่ถูกดึงไปจะถูกส่งย้อนกลับ ไปยังกระบวนการก่อนหน้าเพื่อสั่งการผลิตตามรุ่นและจำนวนที่ลูกค้าดึงไป ซึ่งการดึงสินค้าจากท้าย line ไปบวกกับการส่งข้อมูลย้อนกลับไปยังกระบวนการก่อนหน้าเป็นทอด ๆ นี้จึงเป็นที่มาของคำว่าระบบการผลิตแบบดึง ซึ่งต่างจากระบบผลิตแบบผลักที่เป็นการส่งแผนจากแผนกวางแผนไปให้แต่ละ line การผลิต พอแต่ละ line ได้รับแผนก็จะทำการผลิตให้ได้ตามแผนโดยไม่คำนึงถึงว่ากระบวนการถัดไปหรือ ลูกค้าต้องการอะไร จำนวนเท่าใด ทำให้เกิดเป็น Work In Process (WIP) และ สินค้าคงคลัง กองอยู่เป็นจำนวนมาก ขั้นตอนในการทำกิจกรรมจะเริ่มจากการเขียนแผนภาพ MIFC (Material and Information Flow Chart) และ Stagnation list เพื่อทำการวิเคราะห์สภาพปัจจุบัน ว่ามีจุดหยุดนิ่งของข้อมูลและชิ้นงานตรงจุดใดบ้างและกำหนดเป้าหมายในการปรับ ปรุง โดยใช้ Kanban เป็นสัญลักษณ์ในการสื่อสารข้อมูลระหว่างกระบวนการ และใช้ Lot making post ร่วมกับ chuter ในการเรียงลำดับการผลิต จากนั้นทำการกำหนดพื้นที่สโตร์ท้าย line เตรียมอุปกรณ์แล้วทดลองใช้จริง
ผลจากการทำกิจกรรม Pull System นี้จะสามารถเปลี่ยนระบบการผลิตจากระบบผลักเป็นระบบดึงได้ ลด Lead Time จาก 28 วันให้เป็น 9 วันและลดปริมาณสินค้าคงคลังจาก 7 วันให้เหลือ 3 วัน
เบื้องหลังความสำเร็จของกิจกรรม TPS
- ผู้บริหารระดับสูงของบริษัทให้ความสำคัญกับการทำกิจกรรม โดยลงมาร่วมเป็น Chairman ใน TPS Organize และลงมาร่วมทำงานกับทีมงานอย่างใกล้ชิด ในบทบาทของผู้ขับเคลื่อนกิจกรรมและสนับสนุนให้ทีมงานสามารถทำกิจกรรมได้จน เป็นผลสำเร็จ
- การทำงานที่มีการตั้งเป้าหมายย่อยของแต่ละงานที่ทำ พร้อมทั้งกำหนดผู้รับผิดชอบ และระยะเวลาในการทำที่ชัดเจน ทำให้การประชุมติดตามงานเป็นไปอย่างมีประสิทธิภาพ
- ความมุ่งมั่น ความสามัคคี และการทำงานเป็นทีมของผู้บริหารและทีมงาน TPS ก่อให้เกิดความร่วมมือระหว่างแผนกต่าง ๆ เกิดเป็นการทำงานที่มีลักษณะของ Cross functional ที่ต่างนำเอาความสามารถของแต่ละคนมาใช้ได้อย่างเกิดประโยชน์สูงสุด